ABOUT GE TRANSPORTATION
For decades, GE scientists and engineers have revolutionized locomotive engine design and performance with physical breakthroughs in combustion, electric power and advanced materials. Today, they are leading the digitization of locomotives and the rail network itself, bringing digital horsepower to enable operations at increased speeds and efficiencies of trains on the track.
Bringing AR into a locomotive shop.
This application was designed and built to support Federal Rail Administration safety inspections. The locomotive safety inspection workflow is a 62 step process requiring measurement and analysis of materials. It has to be performed every 92 days and can take a considerable amount of time due to its current process.
KEY ACTIVITIES
01.
Conducting discovery sessions with stakeholders.
02.
Distilling big problems into actionable tasks.
03.
Understanding the activities and challenges of different personas.
04.
Conducting off-site interviews and research.
05.
Creating and brainstorming user flows.
06.
Driving design from sketches to polished designs.
07.
Creating complex prototypes.
08.
Conducting validation alongside subject matter experts and end-users.
PROCESS HIGHLIGHTS
This application was designed and built to support Federal Rail Administration safety inspections. The locomotive safety inspection workflow is a 62 step process requiring measurement and analysis of materials. It has to be performed every 92 days and can take a considerable amount of time.
One of the goals for this project was to find innovative ways on how to expedite the inspection process and ensure a better governance model around the data being acquired. Additionally, how to democratize tribal knowledge around the process in order to expedite on-boarding of new technicians.
Candid shot of one of many Locomotive Shop visits around the Unites States.
Walkthrough and field interviews with subject matter experts. Picture above showcases technician performing a locomotive inspection.
Walkthrough and field interviews with subject matter experts. Picture above showcases locomotive being built.
Field workers performing manual tasks. Picture above shows technician writing height of snowplow using chalk.
Current process done by technicians is starts with pen and paper, then is logged into a computer.
Current process and tasks are assigned and distributed using whiteboard.
Gathering research insights and white-boarding high level concepts.
Expanding concepts into detailed flows.
Translating sketches into high fidelity wireframes.
Documenting functionality and rules to the wireframes.
Final design showcasing landing page for technician.
Locomotive ID is scanned using back camera or smart helmet.
Interface highlights areas that have not been inspected.
Proximity to the locomotive changes the level of detail presented in the UI.
Tasks are broken down into clear sections, making the process easier to follow.
In-context help is offered to allow technicians to operate independently.
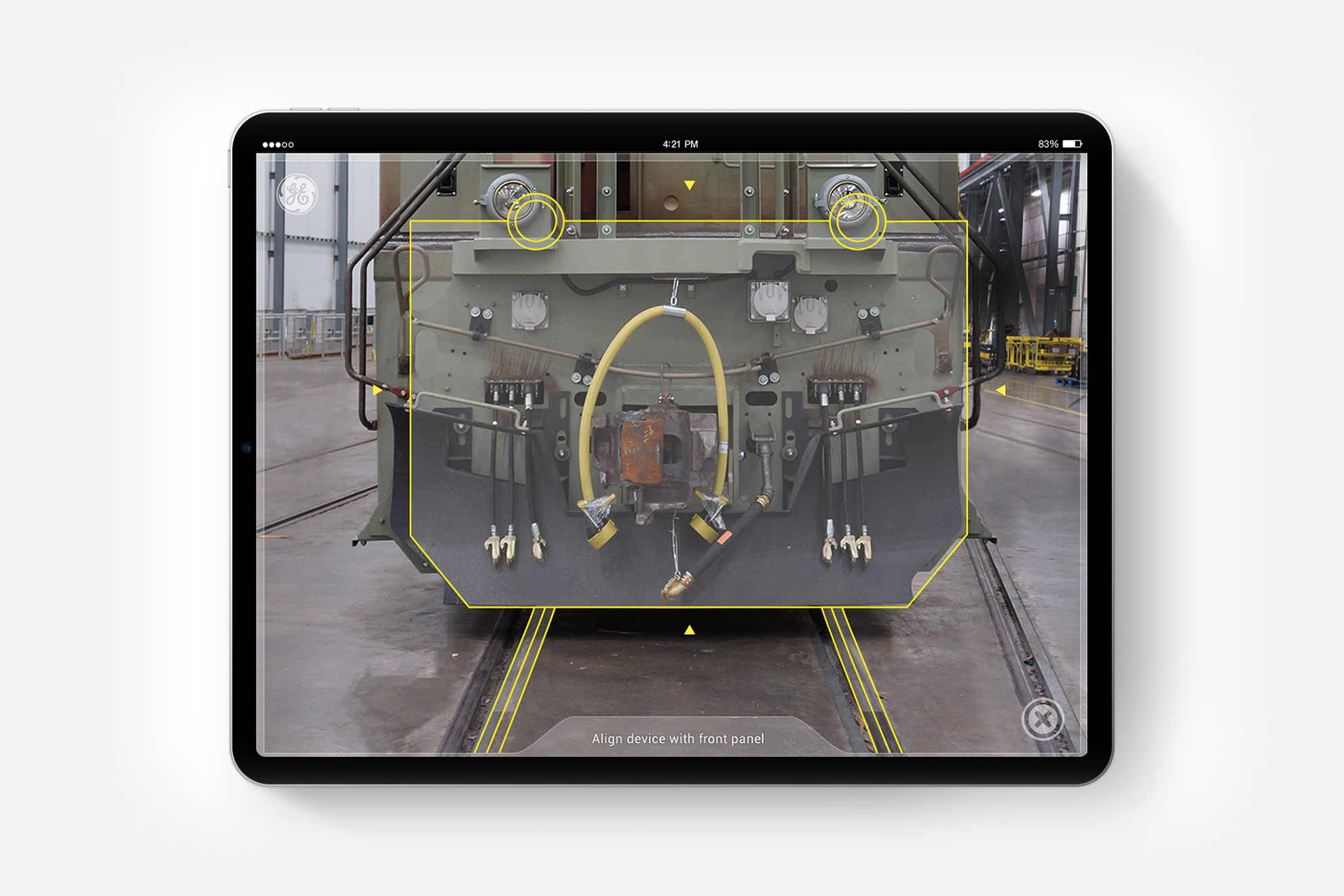

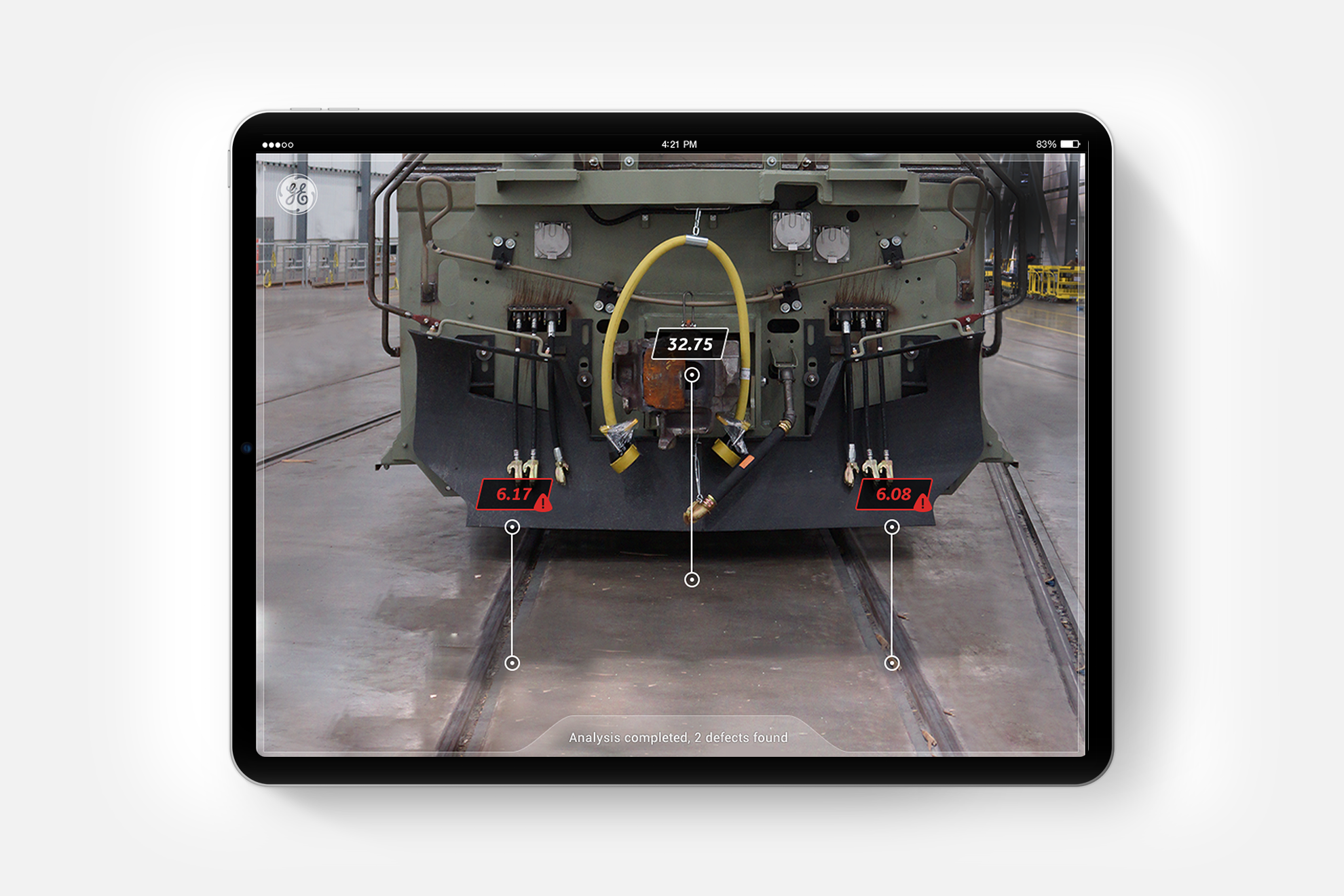
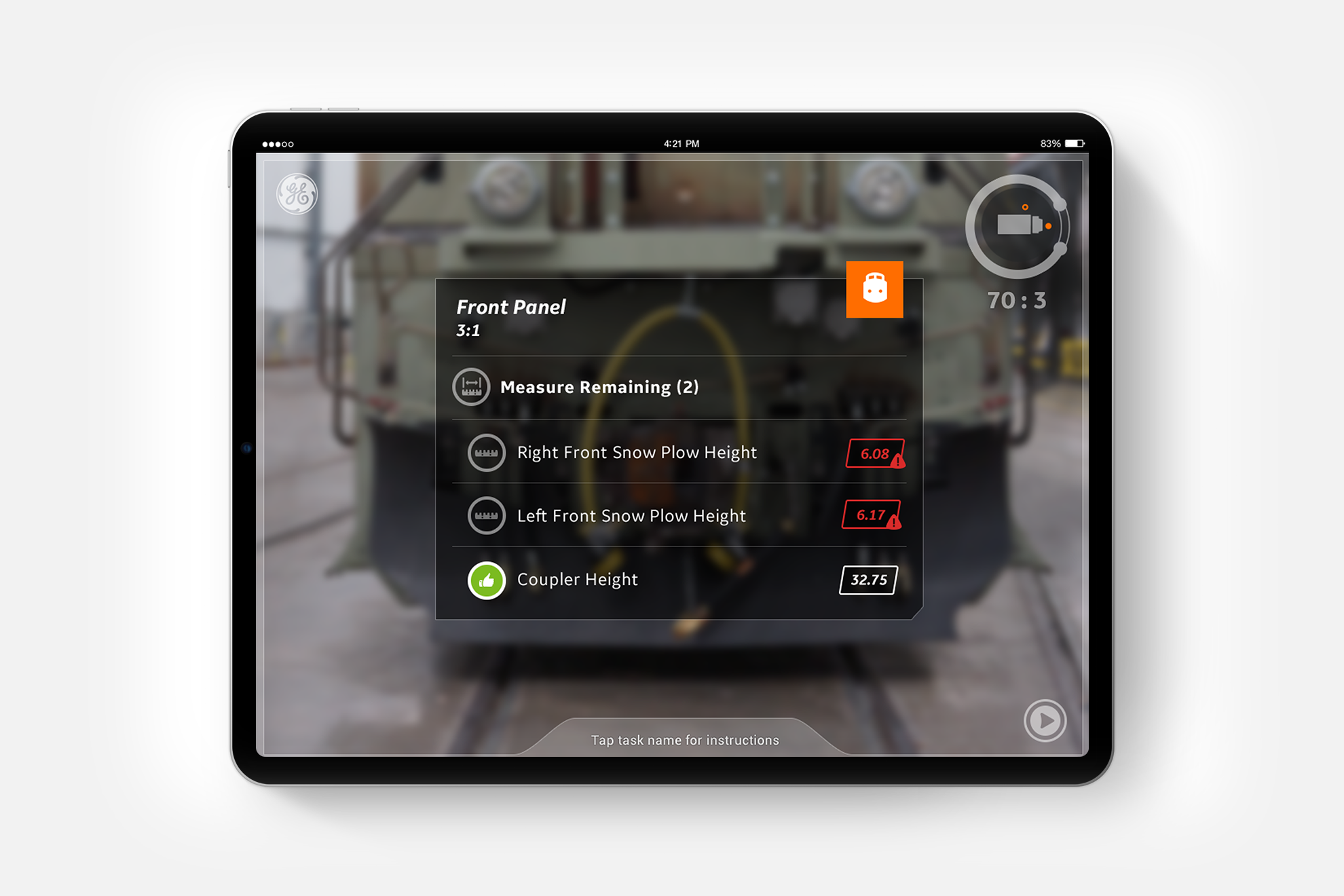

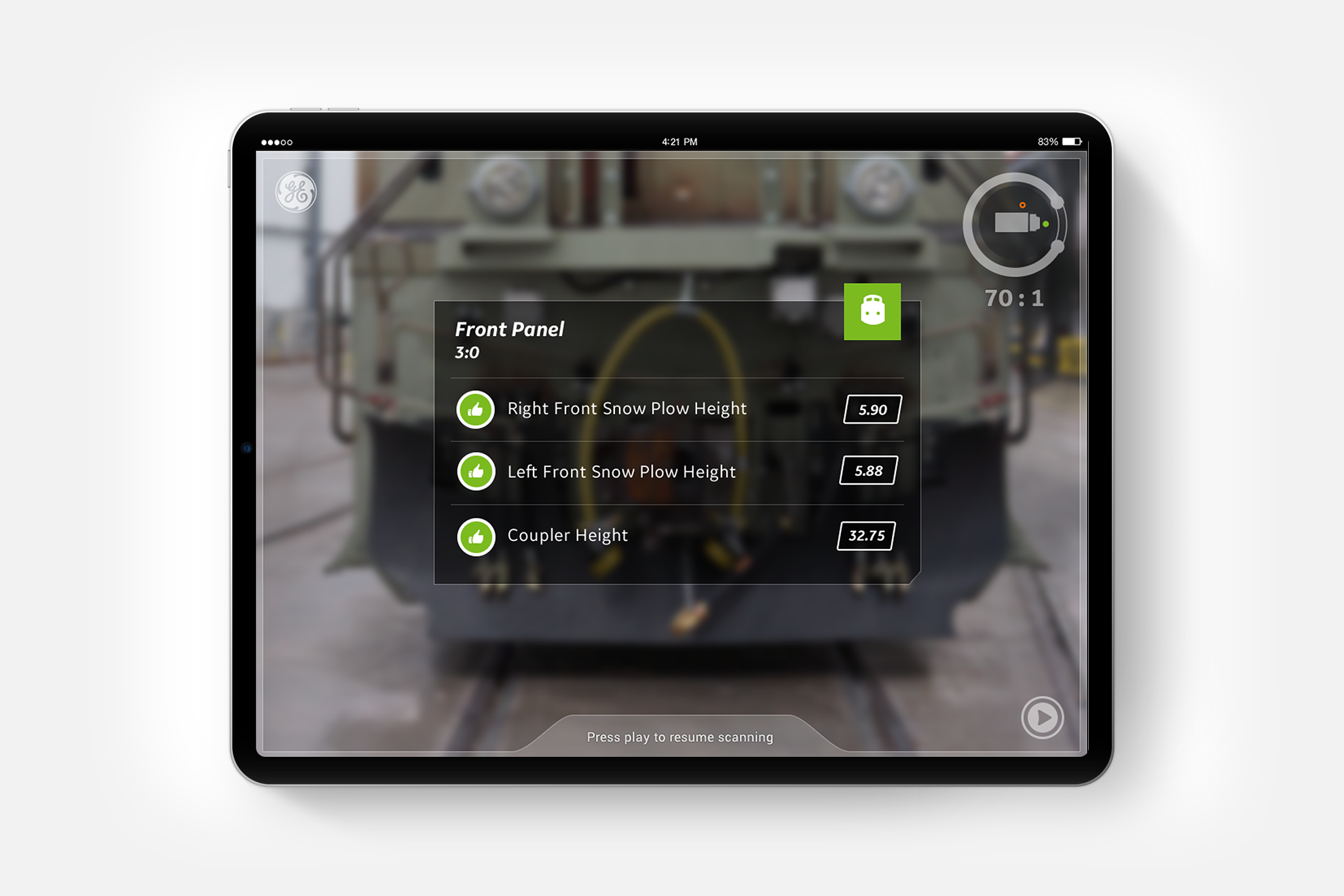
AR enables the automation of manual tasks and removes the need for measuring tools.
In-context help accelerates the learning process.
Smart content educates junior technicians and also serves as on-boarding content.
Picture logging significantly improved accountability and increased reliability.
GE Technician performing inspection utilizing the application.
KEY METRICS
33 Minutes
Average time saved per inspection.
20%+
Potential reduction on number of steps.
$1.2M+
Potential savings/year per shop around process and skilled labor.
Digital
Full digital traceability of the inspection.